Bradbury Flat Book™ -Section 1
READ SECTION 2 OF THE FLAT BOOK™ HERE
The Two Objectives of Leveling
The science of leveling metallic strip has two main goals. The first and obvious objective is to make the appearance of the surface flat and free from ripples. This surface problem is visible and easily measured.
The second objective for leveling is to neutralize the internal stresses that deform parts made from the strip in secondary operations. These internal stresses are not visible and usually show up as twist or bow when a strip is separated from the master sheet in a later operation, such as shearing, stamping, and plasma or laser cutting.
The objective of this booklet is to define these two distinctly different problems and to show how we can correct them through leveling to minimize their effects.
Every metal strip is unique and has different characteristics. Before we explore the solutions, let's discuss how the problems got there in the first place.
The Perfect Coil
During the rolling process at the mill, large crowned rolls are used on the strip to counteract deflection caused by enormous working pressures. This crown on the rolls also helps in steering the strip at high speeds as it is being sized to the target thickness. Hydraulic pressure applied to the ends of these rolls is key to the shape of the final product. If the pressure from roll to material surface is equal across the entire width of the strip, the length of the strip will be exactly the same at all points, and the perfect strip will have been created. In the real world, perfection is rare.
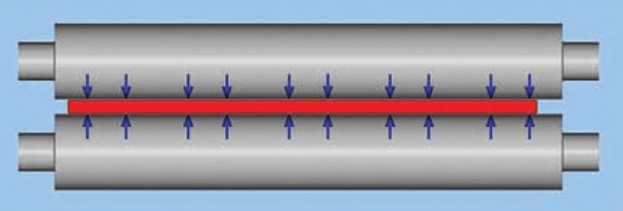
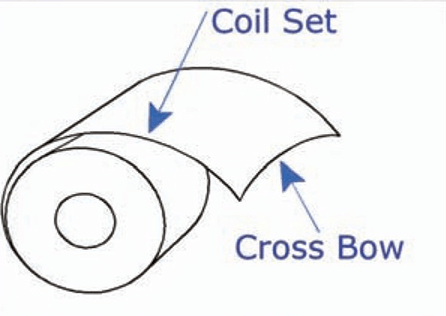
Coil Set and Cross Bow
These two problems appear in every coil and are relatively easy to resolve. Coil Set is caused by winding the coil under tension. This makes the outer surface slightly longer than the inside surface. When Coil Set is pulled lengthwise, the longer outside wrap will cause the shorter inside wrap to curl lengthwise. This effect is called Cross Bow. These two normal coil characteristics are easily removed using a coil straightener or flattener to bend the strip in the opposite direction, equalizing the lengths.
Center Buckle and Edge Wave
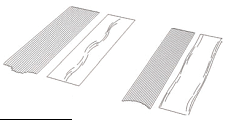
When the roll pressures across the face of the strip are not equal, problems with the shape of the strip occur. The unbalanced pressures will stretch the strip unevenly, leaving ripples in areas across the width.
Let's look at edge wave as an example. Suppose we take a coil with edge wave and cut it into narrow bands. Upon laying these bands side by side on a flat surface - as in the illustration - we would see that the outside bands are longer than the inner bands. The waves we see on the coil edges are an accumulation of extra material. The long outside edge bands can never be made shorter by leveling, so we must stretch the shorter inner bands to even things out. When all of the bands are the same length, we have achieved surface flatness. Center buckle is the inverse of edge wave.
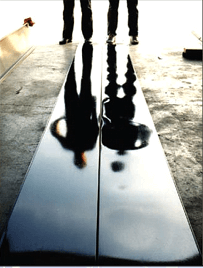
Yield vs Stretch
A review of the properties of metallic strip will make leveler operation more understandable.
Yield
All metals have a yield rating. This yield point refers to the metal's "memory" or its "elastic range" and is a measurement of internal tensions. When flexed within this Elastic Zone, metal will spring back to its previously remembered position. When metal is forced beyond that point, it will enter what is called the Plastic State. This is where the metal is less resistant and becomes more workable. The Tensile Limit, indicated by the arrow at the end of the curve on the Tensile Strength graph (above), is the point where the material will fracture or crack.
Stretch
The Modulus of Elasticity (MOE) is the rating given to different metals to indicate the amount of stretch or elasticity contained in the metal. For example, the MOE for aluminum carries a 3:1 ratio compared to ferrous materials. In other words, aluminum can be forced much farther out of shape before it loses its ability to "spring back" than the same thickness of steel. This suggests that more horsepower is required to level aluminum than is needed to level steel or stainless steel. The MOE of a material is directly related to the amount of "spring back" memory it retains. A material must be stretched beyond this point to lose its memory.
If a leveler is purchased to process both aluminum and steel, it must be sized for aluminum to meet its most demanding horsepower requirement.