Stacking Units
After cooling, insulated metal panels can be stacked in bundles for shipping. From simple drop tables to stackers with programmable end stops that can end justify or pyramid stack, the Bradbury Group can offer a solution that fits your production line requirements. An effective stacker can increase line production by freeing the operator to band and package orders, allowing panel production to continue simultaneously.
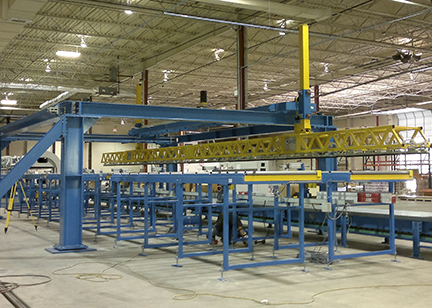
Turnover Units
The turnover unit can be used to flip every other high profiled insulated metal panel, to save space when bundling. It can also be used to flip the last panel on the bundle, to prevent damage to the visible panel face.
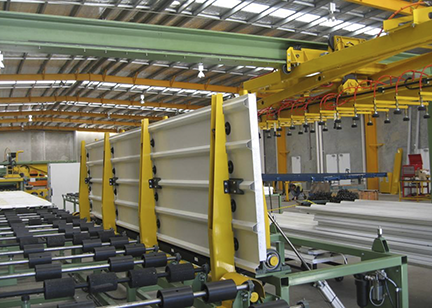
Wrappers/EPS Inserters
Once the bundle is created, it is conveyed to the wrapper station, where EPS blocks or other packing materials can be inserted. The bundle is moved through the Stretch Wrapper which rotates around the whole bundle, including packing materials. Lead/trail end covers can also be applied, to created a completely wrapped bundle. When the insulated metal panel bundle has been fully wrapped, it continues on another conveyor to an unloading area where it can be removed by forklift.
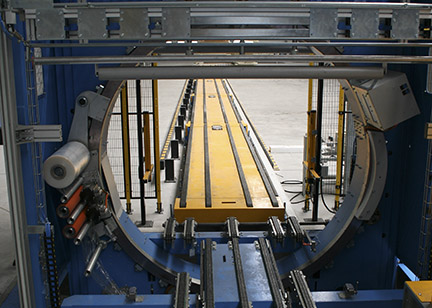